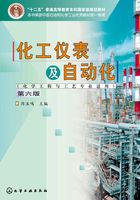
第二节 自动控制系统的基本组成及表示形式
一、自动控制系统的基本组成
自动控制系统是在人工控制的基础上产生和发展起来的。所以,在开始介绍自动控制的时候,先分析人工操作,并与自动控制加以比较,对分析和了解自动控制系统是有裨益的。
图1-2所示是一个液体贮槽,在生产中常用来作为一般的中间容器或成品罐。从前一个工序来的物料连续不断地流入槽中,而槽中的液体又送至下一工序进行加工或包装。当流入量Qi(或流出量Qo)波动时会引起槽内液位的波动,严重时会溢出或抽空。解决这个问题的最简单办法,是以贮槽液位为操作指标,以改变出口阀门开度为控制手段,如图1-2(a)所示。当液位上升时,将出口阀门开大,液位上升越多,阀门开得越大;反之,当液位下降时,则关小出口阀门,液位下降越多,阀门关得越小。为了使液位上升和下降都有足够的余地,选择玻璃管液位计指示值中间的某一点为正常工作时的液位高度,通过改变出口阀门开度而使液位保持在这一高度上,这样就不会出现贮槽中液位过高而溢至槽外,或使贮槽内液体抽空而发生事故的现象。归纳起来,操作人员所进行的工作有三方面,如图1-2(b)所示。

图1-2 液位人工控制
(1)检测 用眼睛观察玻璃管液位计(测量元件)中液位的高低,并通过神经系统告诉大脑。
(2)运算(思考)、命令 大脑根据眼睛看到的液位高度,加以思考并与要求的液位值进行比较,得出偏差的大小和正负,然后根据操作经验,经思考、决策后发出命令。
(3)执行 根据大脑发出的命令,通过手去改变阀门开度,以改变出口流量Qo,从而使液位保持在所需高度上。
眼、脑、手三个器官,分别担负了检测、运算和执行三个作用,来完成测量、求偏差、操纵阀门以纠正偏差的全过程。由于人工控制受到人的生理上的限制,因此在控制速度和精度上都满足不了大型现代化生产的需要。为了提高控制精度和减轻劳动强度,可用一套自动化装置来代替上述人工操作,这样就由人工控制变为自动控制了。液体贮槽和自动化装置一起构成了一个自动控制系统,如图1-3所示。

图1-3 液位自动控制系统
为了完成人的眼、脑、手三个器官的任务,自动化装置一般至少也应包括三个部分,分别用来模拟人的眼、脑和手的功能。如图1-3所示,自动化装置的三个部分分别是:
(1)测量元件与变送器 它的功能是测量液位并将液位的高低转化为一种特定的、统一的输出信号(如气压信号或电压、电流信号等);
(2)自动控制器 它接受变送器送来的信号,与工艺需要保持的液位高度相比较得出偏差,并按某种运算规律算出结果,然后将此结果用特定信号(气压或电流)发送出去;
(3)执行器 通常指控制阀,它与普通阀门的功能一样,只不过它能自动地根据控制器送来的信号值来改变阀门的开启度。
显然,这套自动化装置具有人工控制中操作人员的眼、脑、手的部分功能,因此,它能完成自动控制贮槽中液位高低的任务。
在自动控制系统的组成中,除了必须具有前述的自动化装置外,还必须具有控制装置所控制的生产设备。在自动控制系统中,将需要控制其工艺参数的生产设备或机器叫做被控对象,简称对象。图1-3所示的液体贮槽就是这个液位控制系统的被控对象。化工生产中的各种塔器、反应器、换热器、泵和压缩机以及各种容器、贮槽都是常见的被控对象,甚至一段输气管道也可以是一个被控对象。在复杂的生产设备中,如精馏塔、吸收塔等,在一个设备上可能有好几个控制系统。这时在确定被控对象时,就不一定是生产设备的整个装置。譬如说,一个精馏塔,往往塔顶需要控制温度、压力等,塔底又需要控制温度、塔釜液位等,有时中部还需要控制进料流量,在这种情况下,就只有塔的某一与控制有关的相应部分才是某一个控制系统的被控对象。例如,在讨论进料流量的控制系统时,被控对象指的仅是进料管道及阀门等,而不是整个精馏塔本身。
二、自动控制系统的表示形式
1.方框图
方框图是控制系统或系统中每个环节的功能和信号流向的图解表示,是控制系统进行理论分析、设计中常用到的一种形式。方框图由方框、信号线、比较点、引出点组成。其中,每一个方框表示系统中的一个组成部分(也称为环节),方框内添入表示其自身特性的数学表达式或文字说明;信号线是带有箭头的直线段,用来表示环节间的相互关系和信号的流向;比较点表示对两个或两个以上信号进行加减运算,“+”号表示相加,“-”号表示相减;引出点表示信号引出, 从同一位置引出的信号在数值和性质方面完全相同。作用于方框上的信号为该环节的输入信号,由方框送出的信号称为该环节的输出信号。图1-4为方框图基本组成单元示意图。

图1-4 方框图的基本组成单元示意图
例如图1-3的液位自动控制系统可以用图1-5的方框图来表示。每个环节表示组成系统的一个部分,称为“环节”。两个方框之间用一条带有箭头的线条表示其信号的相互关系,箭头指向方框表示为这个环节的输入,箭头离开方框表示为这个环节的输出。线旁的字母表示相互间的作用信号。

图1-5 液位自动控制系统方框图
图1-3的贮槽在图1-5中用一个“被控对象(简称对象)”方框来表示,其液位就是生产过程中所要保持恒定的变量,在自动控制系统中称为被控变量,用y来表示。在方框图中,被控变量y就是对象的输出。影响被控变量y的因素来自进料流量的改变,这种引起被控变量波动的外来因素,在自动控制系统中称为干扰作用(扰动作用),用f表示。干扰作用是作用于对象的输入信号。与此同时,出料流量的改变是由于控制阀动作所致,如果用一方框表示控制阀,那么,出料流量即为“控制阀”方块的输出信号。出料流量的变化也是影响液位变化的因素,所以也是作用对象的输入信号。出料流量信号q在方框图中把控制阀和对象连接在一起。
贮槽液位信号是测量元件及变送器的输入信号,而变送器的输出信号z进入比较机构,与工艺上希望保持的被控变量数值,即给定值(设定值)x进行比较,得出偏差信号e(e=x-z),并送往控制器。比较机构实际上只是控制器的一个组成部分,不是一个独立的仪表,在图中把它单独画出来(一般方框图中是以○或表示),为的是能更清楚地说明其比较作用。控制器根据偏差信号的大小,按一定的规律运算后,发出信号p送至控制阀,使控制阀的开度发生变化,从而改变出料流量以克服干扰对被控变量(液位)的影响。控制阀的开度变化起着控制作用。具体实现控制作用的变量叫做操纵变量,如图1-3中流过控制阀的出料流量就是操纵变量。用来实现控制作用的物料一般称为操纵介质或操纵剂,如上述中的流过控制阀的流体就是操纵介质。
用同一种形式的方框图可以代表不同的控制系统。例如图1-6所示的蒸汽加热器温度控制系统,当进料流量或温度变化等因素引起出口物料温度变化时,可以将该温度变化测量后送至温度控制器TC。温度控制器的输出送至控制阀,以改变加热蒸汽量来维持出口物料的温度不变。这个控制系统同样可以用图1-5的方框图来表示。这时被控对象是加热器,被控变量y是出口物料的温度。干扰作用可能是进料流量、进料温度的变化、加热蒸汽压力的变化、加热器内部传热系数或环境温度的变化等。而控制阀的输出信号即操纵变量q是加热蒸汽量的变化,在这里,加热蒸汽是操纵介质或操纵剂。

图1-6 蒸汽加热器温度控制系统
必须指出,方框图中的每一个方块都代表一个具体的装置。方框与方框之间的连接线,只是代表方框之间的信号联系,并不代表方框之间的物料联系。方框之间连接线的箭头也只是代表信号作用的方向,与工艺流程图上的物料线是不同的。工艺流程图上的物料线是代表物料从一个设备进入另一个设备,而方框图上的线条及箭头方向有时并不与流体流向相一致。例如对于控制阀来说,它控制着操纵介质的流量(即操纵变量),从而把控制作用施加于被控对象去克服干扰的影响,以维持被控变量在给定值上。所以控制阀的输出信号q,任何情况下都是指向被控对象的。然而控制阀所控制的操纵介质却可以是流入对象的(例如图1-6中的加热蒸汽),也可以是由对象流出的(例如图1-3中的出口流量)。这说明方框图上控制阀的引出线只是代表施加到对象的控制作用,并不是具体流入或流出对象的流体。如果这个物料确实是流入对象的,那么信号与流体的方向才是一致的。
对于任何一个简单的自动控制系统,只要按照上面的原则去作它们的方框图时,就会发现,不论它们在表面上有多大差别,它的各个组成部分在信号传递关系上都形成一个闭合的环路。其中任何一个信号,只要沿着箭头方向前进,通过若干个环节后,最终又会回到原来的起点。所以,自动控制系统是一个闭环系统。
再看图1-5中,系统的输出变量是被控变量,但是它经过测量元件和变送器后,又返回到系统的输入端,与给定值进行比较。这种把系统(或环节)的输出信号直接或经过一些环节重新返回到输入端的做法叫做反馈。从图1-5中还可以看到,在反馈信号z旁有一个负号“-”,而在给定值x旁有一个正号“+”(正号可以省略)。这里正和负的意思是在比较时,以x作为正值,以z作为负值,也就是到控制器的偏差信号e=x-z。因为图1-5中的反馈信号z取负值,所以叫负反馈,负反馈的信号能够使原来的信号减弱。如果反馈信号取正值,反馈信号使原来的信号加强,那么就叫做正反馈。在这种情况下,方框图中反馈信号z旁则要用正号“+”,此时偏差e=x+z。在自动控制系统中都采用负反馈。因为当被控变量y受到干扰的影响而升高时,只有负反馈才能使反馈信号z升高,经过比较到控制器去的偏差信号e将降低,此时控制器将发出信号而使控制阀的开度发生变化,变化的方向为负,从而使被控变量下降回到给定值,这样就达到了控制的目的。如果采用正反馈,那么控制作用不仅不能克服干扰的影响,反而是推波助澜,即当被控变量y受到干扰升高时,z亦升高,控制阀的动作方向是使被控变量进一步升高,而且只要有一点微小的偏差,控制作用就会使偏差越来越大,直至被控变量超出了安全范围而破坏生产。所以控制系统绝对不能单独采用正反馈。
综上所述,自动控制系统是具有被控变量负反馈的闭环系统。它与自动检测、自动操纵等开环系统比较,最本质的区别,就在于自动控制系统有负反馈。开环系统中,被控(工艺)变量是不反馈到输入端的,如化肥厂的造气自动机就是典型的开环系统的例子。图1-7是这种自动操纵系统的方框图。自动机在操作时,一旦开机,就只能是按照预先规定好的程序周而复始地运转。这时煤气炉的工况如果发生了变化,自动机是不会自动地根据炉子的实际工况来改变自己的操作的。自动机不能随时“了解”炉子的情况并依此改变自己的操作状态,这是开环系统的缺点。反过来说,自动控制系统由于是具有负反馈的闭环系统,它可以随时了解被控对象的情况,有针对性地根据被控变量的变化情况而改变控制作用的大小和方向,从而使系统的工作状态始终等于或接近于所希望的状态,这是闭环系统的优点。

图1-7 自动操纵系统方框图
2.管道及仪表流程图
管道及仪表流程图(Piping and Instrumentation Diagram,P&ID)是自控设计的文字代号、图形符号在工艺流程图上描述生产过程控制的原理图,是控制系统设计、施工中采用的一种图示形式。管道及仪表流程图在工艺流程图的基础上,按其流程顺序,标出相应的测量点、控制点、控制系统及自动信号与连锁保护系统等。在控制方案确定以后,由工艺人员和自控人员共同研究绘制。
图1-8是乙烯生产过程中脱乙烷塔的工艺管道及控制流程图。为了说明问题方便,对实际的工艺过程及控制方案都做了部分修改。从脱甲烷塔出来的釜液进入脱乙烷塔脱除乙烷。从脱乙烷塔塔顶出来的碳二馏分经塔顶冷凝器冷凝后,部分作为回流,其余则去乙炔加氢反应器进行加氢反应。从脱乙烷塔底出来的釜液部分经再沸器后返回塔底,其余则去脱丙烷塔脱除丙烷。

图1-8 脱乙烷塔的工艺管道及控制流程图
在绘制P&ID图时,图中所采用的图例符号要按有关的技术规定进行,如可参见化工行业标准HG/T 20505—2000《过程测量和控制仪表的功能标志及图形符号》。下面结合图1-8对其中一些常用的统一规定做简要介绍。
(1)图形符号
①测量点(包括检出元件、取样点)。是由工艺设备轮廓线或工艺管线引到仪表圆圈的连接线的起点,一般无特定的图形符号,如图1-9所示。图1-8中的塔顶取压点和加热蒸汽管线上的取压点都属于这种情形。

图1-9 测量点的一般表示方法
必要时,检测元件也可以用象形或图形符号表示。例如流量检测采用孔板时,检测点也可用图1-8中脱乙烷塔的进料管线上的符号表示。
②连接线。通用的仪表信号线均以细实线表示。连接线表示交叉及相接时,采用图1-10的形式。必要时也可用加箭头的方式表示信号的方向。在需要时,信号线也可按气信号、电信号、导压毛细管等采用不同的表示方式以示区别。

图1-10 连接线的表示法
③仪表(包括检测、显示、控制)的图形符号。仪表的图形符号是一个细实线圆圈,直径约10mm,对于不同的仪表安装位置的图形符号如表1-1所示。
表1-1 仪表安装位置的图形符号表示

对于处理两个或两个以上被测变量,具有相同或不同功能的复式仪表时,可用两个相切的圆或分别用细实线圆与细虚线圆相切表示(测量点在图纸上距离较远或不在同一图纸上),如图1-11所示。

图1-11 复式仪表的表示法
(2)字母代号 在控制流程图中,用来表示仪表的小圆圈的上半圆内,一般写有两位(或两位以上)字母,第一位字母表示被测变量,后继字母表示仪表的功能,常用被测变量和仪表功能的字母代号见表1-2。
表1-2 被测变量和仪表功能的字母代号

注:“供选用的字母(例如表中Y),指的是在个别设计中反复使用,而本表内未列入含意的字母。使用时字母含意需在具体工程的设计图例中作出规定,第一位字母是一种含意,而作为后继字母,则为另一种含意。”
以图1-8的脱乙烷塔控制流程图,来说明如何以字母代号的组合来表示被测变量和仪表功能的。塔顶的压力控制系统中的PIC-207,其中第一位字母P表示被测变量为压力,第二位字母I表示具有指示功能,第三位字母C表示具有控制功能,因此,PIC的组合就表示一台具有指示功能的压力控制器。该控制系统是通过改变气相采出量来维持塔压稳定的。同样,回流罐液位控制系统中的LIC-201是一台具有指示功能的液位控制器,它是通过改变进入冷凝器的冷剂量来维持回流罐中液位稳定的。
在塔的下部的温度控制系统中的TRC-210表示一台具有记录功能的温度控制器,它是通过改变进入再沸器的加热蒸汽量来维持塔底温度恒定的。当一台仪表同时具有指示、记录功能时,只需标注字母代号“R”,不标“I”,所以TRC-210可以同时具有指示、记录功能。同样,在进料管线上的FR-212可以表示同时具有指示、记录功能的流量仪表。
在塔底的液位控制系统中的LICA-202代表一台具有指示、报警功能的液位控制器,它是通过改变塔底采出量来维持塔釜液位稳定的。仪表圆圈外标有“H”、“L”字母,表示该仪表同时具有高、低限报警,在塔釜液位过高或过低时,会发出声、光报警信号。
(3)仪表位号 在检测、控制系统中,构成一个回路的每个仪表(或元件)都应有自己的仪表位号。仪表位号是由字母代号组合和阿拉伯数字编号两部分组成。字母代号的意义前面已经解释过。阿拉伯数字编号写在圆圈的下半部,其第一位数字表示工段号,后续数字(二位或三位数字)表示仪表序号。图1-8中仪表的数字编号第一位都是2,表示脱乙烷塔在乙烯生产中属于第二工段。通过控制流程图,可以看出其上每台仪表的测量点位置、被测变量、仪表功能、工段号、仪表序号、安装位置等。例图1-8中的PI-206表示测量点在加热蒸汽管线上的蒸汽压力指示仪表,该仪表为就地安装,工段号为2,仪表序号为06。而TRC-210表示同一工段的一台温度记录控制仪,其温度的测量点在塔的下部,仪表安装在集中仪表盘面上。