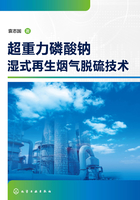
1.2 烟气脱硫技术应用现状
烟气脱硫(Flue Gas Desulfurization)是控制酸雨和SO2污染的最有效的技术手段,也是世界上开展的最大规模商业化应用的脱硫方法。据美国国家环保局统计,各国研究、开发的烟气脱硫技术已超过200多种,但真正应用到工业化中的仅有20多种。
烟气脱硫技术有多种分类,如按脱硫工艺分为干法、半干法和湿法,按脱硫产物的处理方法分为回收法和抛弃法;按吸收机理分为化学法和物理法;按脱硫剂分为钙法、钠法、氨法、双碱法和磷酸盐法等;按吸收剂是否可再生和循环使用情况分为再生法和非再生法。下面对已工业化应用的主要烟气脱硫方法(按脱硫剂分类)特点进行简要总结,如表1-2所列。
表1-2 主要烟气技术的特点


从表1-2可以看出,各种烟气脱硫方法都存在一定的优势和缺点,具体选用什么样的脱硫方法需要结合市场和当地资源情况来选择。因而,不同国家或地区,应用的脱硫方法也不尽相同。
1.2.1 国外烟气脱硫技术
20世纪70年代末,湿式石灰/石灰石-石膏法脱硫技术在美国、日本、德国等发达国家基本成熟,并大规模推向市场,90年代中后期,这些国家的脱硫市场逐渐饱和。近年来,不断对湿法烟气脱硫工艺进行了改进和开发,如双碱法、千代田法、氧化镁法、氨酸法等烟气脱硫工艺均进行了工业化应用。2000年,美国、日本、德国等发达工业国家就已经完成200610MW的电厂烟气脱硫净化。主要采用的烟气脱硫技术有:①湿式烟气脱硫技术,据国际能源机构煤炭研究组织调查表明,占安装烟气脱硫机组总容量的85%左右;②喷雾干燥烟气脱硫技术,约占8.4%;③吸收剂再生烟气脱硫技术,约占3.4%;④炉内喷射脱硫剂/增温活化脱硫技术,约占1.9%;⑤海水脱硫技术;⑥烟气循环流化床脱硫技术等。这些技术及其装备绝大部分集中在美国、日本以及德国。
(1)日本
日本是世界上最早大规模应用烟气脱硫的国家,从20世纪60年代开始大规模应用,SO2污染在70年代中后期就得到了基本控制。80年代以来,日本对美国、德国及发展中国家出口烟气脱硫技术及设备。
因日本资源匮乏,烟气脱硫主要采用湿法回收工艺,占整个脱硫工艺的98%左右,其中湿式石灰石-石膏法应用最多(约占50%),且回收副产物石膏,日本建筑所用石膏大都来自脱硫石膏,其投资和运行费用较高,运行操作需要严格控制;其次是亚铵法(约占24%),回收副产物肥料硫酸铵;双碱法(约占16%),可回收副产物石膏。日本掌握烟气脱硫技术的企业主要有川崎重工、三菱重工、巴威-日立、日立造船、千代田、荏原等公司,先后向我国出口了湿式石灰石-石膏法、喷气沸腾简易脱硫法、炉内喷钙加湿活化法、气悬浮体吸收法、旋转喷雾法等多种脱硫工艺及设备。
(2)美国
美国的烟气脱硫技术研究自20世纪70年代初开始,特别是1978年重新修改了环境法规,否决了高烟囱排放后,烟气脱硫技术得到了迅速的发展。尤其是在1986~1995年期间,新安装的燃煤发电机组32815MW,均安装了烟气脱硫装置,使得烟气脱硫容量占总装机量从18.77%上升到了27%。
美国的石灰石资源丰富,湿式石灰/石灰石-石膏法占90%以上,副产物石膏基本抛弃;其次是碳酸钠法和双碱法。从20世纪80年代以来,为降低投资和运行费用,研发了炉内直接喷射石灰石和喷雾干燥烟气脱硫技术。目前,美国仍在不断开发脱硫效率高、占地小、投资省、适合电厂改造的烟气脱硫技术。
(3)欧洲
欧洲烟气脱硫技术发展最为迅速的德国,在引进美国、日本等发达国家先进技术的同时,立足于本国技术开发,于20世纪70年代末,开始在电站锅炉上安装烟气脱硫装置。德国90%以上的烟气脱硫方法是湿式石灰/石灰石-石膏法,其中大部分采用回收工艺,工业用石膏的75%来自脱硫石膏。目前,德国加装脱硫、脱硝设备的电厂发电量达106MW·h。
此外,北欧的挪威、丹麦、芬兰等对烟气脱硫技术也开展了大规模研究,已开发了半干法脱硫、旋转喷雾干燥法脱硫、炉内喷钙+尾部烟道增湿活化法脱硫、双循环流化床烟气脱硫、海水脱硫等一些先进脱硫工艺,并在本国和国外进行了推广应用。
总的来看,湿式石灰/石灰石-石膏脱硫技术是国外烟气脱硫应用最为普遍的技术,约占40%,包括回收和抛弃两种工艺;其次是以钠法、镁法为代表的烟气脱硫技术。这些技术的优点是脱硫率可达90%以上,适应性强,脱硫剂来源广,能适应锅炉负荷的变化;缺点是操作复杂,易产生堵塞和设备腐蚀,设备占地面积大,投资大(占电厂投资的20%以上),系统电耗大,运行费用高,发电成本增加18%~22%。针对上述缺点进行了某些改进和优化,如通过加入氧化剂,实行强制氧化,以减少吸收塔和附属设备的体积、降低投资和运行费用;选用耐腐蚀材料,延长设备使用寿命。但这些改进未能从根本上解决问题,仍是以高投入、高消耗、低效益为特征的传统污染治理模式。
1.2.2 国内烟气脱硫技术
我国在烟气脱硫技术方面的研究和实践开始较晚,从20世纪90年代才开始引进国外技术,在中小型电厂建立烟气脱硫示范工程,到2002年之后开始在新建火电机组上大规模实施烟气脱硫。特别是最近十多年来,在环境和国家政策、法规压力下,国家对环保措施投入增加,很多电厂、热力公司、冶炼厂都相继引进或建立烟气脱硫装置,其中燃煤机组烟气脱硫装置占煤电机组的比例由20世纪初的2%上升到了现在的90%以上,装设烟气脱硫装置的速度超过世界任何国家。期间,国内的脱硫公司快速发展到了200余家,由最初的靠引进先进技术,然后消化吸收再创新,逐渐形成了自己的特点。国内实力较强的烟气脱硫公司基本都是这种模式发展起来的,如北京博奇引进日本川崎的技术,国电龙源引进德国SteinmÜller技术,武汉凯迪引进美国B&W技术,中电投远达引进奥地利AEE和日本三菱的技术,福建龙净和上海龙净等引进德国Bischof技术。
国家环境保护部2013年第24号公告公布了全国已建成投运的燃煤机组脱硫脱硝设施、钢铁烧结机及球团脱硫设施企业名单和脱硫方法、数量、规模。其中,全国燃煤脱硫机组共4659台,总装机容量7.18×108kW;钢铁烧结机脱硫设施389台,烧结机总面积6.32×104m2;钢铁球团脱硫设施44台,球团年生产能力1461万吨。对其中列出的全国燃煤脱硫机组数据统计出脱硫方法及其应用比例进行分析,如表1-3所示。
表1-3 全国燃煤机组脱硫方法统计

由表1-3可以看出,国内的燃烧机组脱硫方法主要集中在湿法烟气脱硫,超过整个装机容量的95%;尤其是湿式石灰石/石灰-石膏法,占整个脱硫装机容量的82.67%;其次是炉内喷钙+尾部湿法脱硫、海水脱硫和双碱法等。通过上述对脱硫方法与技术的分析,不难发现我国应用的烟气脱硫技术还存在如下问题。
(1)投资成本高
一些发达国家对SO2治理往往采用高投入、高消耗的模式,然而由于我国烟气脱硫的研究起步较晚,很多技术和设备都依赖进口,特别是系统复杂,设备体积庞大、占地面积大、导致了极高的投资成本。如我国最早的湿法烟气脱硫示范项目重庆珞璜电厂引进的“石灰石-石膏法”烟气脱硫装置,仅投资就高达4000万美元,运行费用每年约4000万元人民币,脱除1吨SO2需要约1100元。
(2)运行费用高
目前,主要采用的石灰/石灰石-石膏法烟气脱硫技术存在系统复杂,工艺长,动力消耗大,尤其是存在设备易积垢、堵塞、腐蚀和磨损等缺点,导致维护以及管理成本居高不下。特别是针对最近提出的超低排放标准,需要增加喷淋层、液气比和钙硫比,导致运行费用大大增加,石灰石资源利用率降低和固体废弃物大量堆积。
(3)脱硫副产物出路难
采用湿式脱硫法处理烟气将产生大量的脱硫副产物石膏,而我国天然石膏资源丰富,价格低廉。虽然上海等较发达地区出台了一系列针对脱硫石膏再利用的优惠政策,但更多的脱硫石膏因含水量高、质量差、含氯离子浓度高等,仍旧难以有效利用。目前,绝大部分脱硫石膏还是以堆储为主,已成为火电厂第二大固体废物,如重庆珞璜电厂一期工程,每年就有25万吨固体物排放,不仅占用土地资源和浪费大量的硫资源,而且将来对环境产生不可估量的影响。
(4)脱硫技术完全国产化进程慢
国产化主要包括设备国产化和技术国产化,其目的是降低脱硫成本,其中,尤以技术国产化最为关键。我国现有的脱硫技术与设备绝大多数由国外引进,虽然国内已有能力制造大部分设备,但在产品可靠性、耐用性等方面与国外产品相比还具有差距。而国内从事烟气脱硫领域的公司虽然具备中小型烟气脱硫工程的设计、施工、成套设备和调试等总承包能力,但仍旧缺乏自主知识产权,特别是大型设备的运转效果和可靠性难以得到有效保证。
因而,国内烟气脱硫技术的创新、开发和研究任重而道远,还需要大量的人力和物力的投入,也为新型脱硫技术的开发应用提供了良好前景。
从世界各国主要烟气脱硫技术的应用情况来看,应用最多的是湿法烟气脱硫技术,其中以石灰/石灰石-石膏法为主,超过1/2以上。该方法的吸收剂不可再生,吸收剂消耗大,副产品脱硫石膏含水量高、纯度低,对其综合利用率低,再加工利用成本比较高,根据各个国家或地区的资源情况不同,有的直接抛弃或填埋,如美国,因石膏资源相对比较丰富;有的采用回收法处理,如日本等国家,主要因为人口密度大、资源相对匮乏。
总的来看,现已工业化应用的湿法脱硫工艺绝大多数采用碱性浆液或溶液作为吸收剂,具有脱硫效率高(能够达到90%以上,但很难经济地达到目前新的排放标准)、吸收剂利用效率高、反应速度快等优点,但也普遍存在投资和运行维护费用高、腐蚀严重、特别是石灰/石灰石-石膏法还易造成堵塞、二次污染等问题。相比之下,湿式再生烟气脱硫技术比抛弃法更经济、环保,尤其是把烟气中SO2转化为高浓度SO2、硫磺黄、浓硫酸等副产品更符合发展循环经济,促进可持续发展战略的需要,并且避免了二次污染,实现了变废为宝的回收法治理,此类方法将会成为未来发展的趋势。所以近年来国内外学者结合湿法烟气脱硫的优势,一直致力于湿式再生烟气脱硫、回收治理工艺的研究与开发。