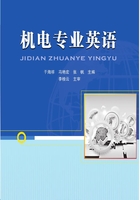
Module 1 Foundation of Mechanical Technology
Task 1 Mechanical Engineering
Part A
Text
1.1.1 Drawing
1.Engineering drawing
Typical drawings in machine manufacturing are classified as part drawings and assembly drawings.
(1)Part drawings(Fig.1-1-1)

Fig.1-1-1 Part drawings
Part drawings are frequently used as instructing for manufacture and inspecting for the parts.An integrated part drawing should include a set of drawings,overall dimensions,necessary technical requirements and full contents of title block.
①A set of drawings:some representation can be given to properly show the internal and external shape of the part.
②Overall dimensions:specifying the requirements for manufacture and inspection of the integrity.
③Necessary technical requirements:codes,symbols and notes are used to describe the essential technical requirements in the process of manufacture,inspection and assembly,such as surface roughness,tolerance,heat treatment,case treatment and the like.
④Full contents of title block:including the part name,materials,drawing number,scale and signature of responsible individual.
(2)Assembly drawings(Fig.1-1-2)
Assembly drawings are used in explaining machines or components.In mechanical design,part drawings are usually related to the assembly drawing which indicates the working principle and structure of a machine or component.In the process of machine manufacturing,the drawings are to allow machining of the metal based on the part drawing and assembling to create a unit or a machine according to the assembly drawing.

Fig.1-1-2 Assembly drawings
2.Representation of machine elements
Mechanical drawingsin national standards are restricted to those which specify the view,sectional view and broken sectional view to represent the structures and shapes.
Views are projection drawings of the object.Typical views include basic views,directional views,partial views and oblique views.Basic views include upward view,front view,vertical view,right view,left view and back view,as shown in Fig.1-1-3.The number of views is always six,four and three,four is the typical views.
Sectional views(Fig.1-1-4)are used to show the internal structure of the object with a dash line.When parts have complex internal geometries,knowing the interior is as important as knowing the exterior,you can use sectioning technique to “cut sections” across the object to show internal details.We divide sectional views into full sectional views,half sectional views and partial sectional views.
Broken sectional views(Fig.1-1-5)are supposed to be sectional plane at a point somewhere on the machine element drawn only section graphics.We divide them into removed broken sectional view and superposition sectional view.

Fig.1-1-3 Basic views

Fig.1-1-4 Sectional views
For expressing the structure and size of a component distinctly,we put a component into a three-plane projection system,and acquire the three-dimensional drawing in the three projection plane.The basic principle is indicated as equal length in the front view and vertical view,equal height in the front view and left view,equal width in the vertical view and left view.
The axonometric drawing is used for complementing the outline of the body.There are two kinds of axonometric drawings:positive isometric and oblique two.

Fig.1-1-5 Broken sectional views
1.1.2 Metals and It’s Properties
1.Metals
Metals are divided into two general groups:ferrous metals and nonferrous metals.The major types of ferrous metals are cast iron,carbon steels,alloy steels and tool steels.
The three primary types of cast iron are gray cast iron,white cast iron,and malleable cast iron.Gray cast iron is primarily used for cast frames,automobile engine blocks,hand-wheel and cast housings.White cast iron is hard and wear resistant and is used for parts such as train wheels.Malleable cast iron is a tough material used for tools such as pipes and wrenches.Generally,cast irons have very good compressive strength,corrosion resistance,and good machine-ability.The main disadvantage of cast iron is its natural brittleness.
The three principal types of carbon steel used in industry are low,medium,and high carbon steel.The percentage of carbon is the most important factor in determining the mechanical properties of each type of carbon steel.Low carbon contains between 0.05% and 0.30% carbon and is primarily used for parts that do not require great strength,such as chains,bolts,nuts,and pipes.Containing between 0.30% and 0.50% carbon,medium carbon steel is used for part that required great strength than is possible with low carbon steel,such as gears,crankshafts,machine parts and axles.Containing between 0.50% and 1.70% carbon,high carbon steel is used for parts that require hardness and strength,such as files,knives,drills,razors,and woodworking tools.
Alloy steels are basically carbon steels with elements added to modify of change the mechanical properties of the steel.
Tool steels are a special grade of alloy steels used for making a wide variety of tools.
Nonferrous metals are those metals whose major element is not iron.As compared to ferrous metals,the list of nonferrous metals is,of course,long and complex.The major families of nonferrous metals,such as aluminum and aluminum alloys,copper and copper alloys,magnesium and magnesium alloys,titanium and titanium alloys.
2.Properties of metals
The properties of metals are the characteristics that determine how the metal will react under varying conditions.The two principal types of properties are physical and mechanical.Physical properties are those fixed properties that are determined naturally and cannot be changer,such as weight,mass,color,and specific gravity.Mechanical properties,on the other hand,are those properties of metal that can be changed or modified to meet a particular need,such as strength,hardness,wear resistance,toughness,plasticity,and brittleness.
(1)Strength
Strength is a property of metal that allows it to resist permanent change in shape when loads are applied.There are four types or forms of strength you should know are:tensile strength,shear strength,compressive strength,and ultimate strength.
(2)Hardness
Hardness is the ability of a metal to resist indentation or penetration.Several different methods are used to measure the hardness of a metal;however,the two primary methods,or test,used by industry are the Brinell and Rockwell hardness tests.
(3)Wear resistance
Wear resistance is the ability of a metal to resist abrasion.In most cases,the harder the metal,the better it resists wear.
(4)Toughness
Toughness is the ability of a metal to resist,or absorb,sudden shocks of loads without breaking.
(5)Plasticity
Plasticity is the ability of a metal to be extensively deformed without fracture or rupture.
(6)Brittleness
Brittleness is the property of a metal that causes it to fracture rather than deform when loads are applied.Brittleness is the opposite of plasticity.
1.1.3 Heat Treatment of Metals
Heat treatment is a process of controlled heating and cooling of a metal to achieve a characteristics change in the properties.Heat treatment curve is shown as Fig.1-1-6.The five common heat-treating operations performed on steels are annealing,normalizing,hardening,tempering,and case hardening.Most nonferrous metals can be annealed,and some are harden-able by heat treatment.However,nonferrous metals are not normalized,tempered,or case hardened.
Annealing is a process used to soften metals that is generally performed on hardened parts that,for some reason,must be machined.Purposes of annealing:remove hardness;increase malleability;increase ductility;improve machine-ability;refine grain structure.
Normalizing is a process used to reduce the internal stresses in a metal caused by machining or forming.Purposes of normalizing:relieve stresses;produce normal grain size and structure;place steels in the best condition for machining;lessen distortion in heat treating.

Fig.1-1-6 Heat treatment curve
Hardening is the process of increasing the strength,hardness,and wear resistance of a metal.Purposes of hardening:increase hardness,strength and wear resistance.
Tempering relieves some of the stressed caused by rapid cooling in the hardening process.Purposes of tempering:reduce hardness to desired level;increase shock resistance and impact strength;reduce brittleness;relieve stresses caused by rapid cooling.
Case hardening is a process of producing a hard case,or shell,around a low carbon steel part by adding carbon to its surface.This process is well suited for parts that need a hard,wear-resistance surface and a tough inner core.Gears,sprockets are typical example of parts that are case hardened.
1.1.4 Machine Elements
1.Machine and parts
However simply,any machine is a combination of individual components generally referred to as machine elements or parts.Thus,if a machine is completely dismantled,a collection of simple parts such as nuts,bolts,springs,gears,cams and shafts,etc.—the building block of all machinery.
The most common example of a machine element is a gear.Gears are designed to transfer rotary motion from one shaft to another.The speed of the motion is increased or decreased by changing the size of the drive gear and the driven gear.
2.Name of different gear parts(Fig.1-1-7)
(1)Number of teeth
The total average number of gear teeth on the gear circumference is called the number of teeth,which is symbolized as Z.
(2)Addendum circle,dedendum circle
The space between the adjacent two teeth is called the keywall.The circle over the bottom of all keywalls are called dedendum circle,whose radius is symbolized as rf.The circle over the top of all gear teeth are called addendum circle,whose radius is symbolized as ra.The addendum circle of the external gear is bigger than its dedendum circle,the addendum circle of the internal wheel is smaller than its dedendum circle.

Fig.1-1-7 Name of different gear parts
(3)Reference circle
To design or manufacture,a circle is set artificially.The modulus of the circle is a standard value.Also the pressure angle is a standard value.The circle is called the reference circle.
(4)Tooth addendum,tooth dedendum,whole depth
The radial distance between the reference circle and the addendum circle is called the tooth addendum,which is symbolized as ha.
The radial distance between the reference circle and the dedendum circle is called the tooth dedendum,which is symbolized as hf.
The radial distance between the addendum circle and the dedendum circle is called the whole depth,which is symbolized as h.
3.Gear types and applications
There are several kinds of gears used in modern machinery.Some of those are spur gears,helical gears,gear racks,bevel gears,worm and worm wheel.
Spur gears(Fig.1-1-8)are the most widely used style of gears and are used to transmit rotary motion between parallel shafts,while maintaining uniform speed and torque.The involute tooth form,being the simplest to generate,permits high manufacturing tolerances to be attained.

Fig.1-1-8 Spur gears
Helical gears(Fig.1-1-9)are similar to spur gears with the exception that the teeth are cut at an angle to the axis of the shaft—the helix angle.The helix cut creates a wider contact area enabling higher strengths and torques to be achieved.
Bevel gears(Fig.1-1-10)are used solely to transmit rotary motion between intersecting shafts.

Fig.1-1-9 Helical gears

Fig.1-1-10 Bevel gears
New Words and Phrases
roughness [rʌfnəs] n.粗糙,粗糙的地方
tolerance [ˈtɒlərəns] n.公差,限度
sectional [ˈsekʃənl] adj.断面的,局部的,部分(地区)的
oblique [əˈbliːk] adj.斜,倾斜的
gray [greɪ] adj.灰色的,灰白头发的
malleable [ˈmæliəbl] adj.可锻造的,有延展性的,韧性的
razor [ˈreɪzə(r)] n.剃刀,刮面刀
magnesium [mægˈniːziəm] n.[化]镁(金属元素)
titanium [tɪˈteɪniəm] n.[化]钛
characteristic [ˌkærəktə'rɪstɪk] n.性质,特性,特征,特色
tensile [ˈtensaɪl] adj.拉力的,张力的,可伸展的,可拉长的
shear [ʃɪə(r)] vi.剪切,修剪,穿越,[力]切变
ultimate [ˈʌltɪmət] adj.极限的,最后的,最大的,首要的
brinell [brinel] n.(布氏)压痕
abrasion [əˈbreɪʒn] n.磨损,擦伤处,磨蚀
fracture [ˈfræktʃə(r)] n.破裂,断裂
rupture [ˈrʌptʃə(r)] n.断裂,破裂
annealing [əˈniːlɪŋ] v.退火,退火(anneal的现在分词)
normalizing [ˈnɔ:məlaɪzɪŋ] n.正火
tempering [ˈtempərɪŋ] v.回火,钢化
malleability [ˌmælɪəˈbɪləti] n.有延展性,柔韧性,柔顺
distortion [dɪˈstɔːʃn] n.扭曲,变形,失真,畸变
dedendum [dɪˈdendəm] n.齿根,齿根高
addendum [əˈdendəm] n.附录,[机](齿轮的)齿顶(高)
engineering drawing 工程图纸
assembly drawing 装配图
partial view 局部视图
oblique view 斜视图
cast iron 铸铁
wear resistance 耐磨性
nonferrous metal 有色金属
addendum circle 齿顶圆
dedendum circle 齿根圆
spur gears 直齿圆柱齿轮
helical gears 斜齿轮
Exercises
Ⅰ.Match column A with column B.

Ⅱ.Mark the following statements with T(true)or F(false).
( )1.Directional views include full sectional views,half sectional views and partial sectional views.
( )2.The axonometric drawing is used for complementing the outline of the body.
( )3.Metals are divided into three general groups:gray cast iron,white cast iron,and malleable cast iron.
( )4.Brittleness is the opposite of plasticity.
( )5.Tempering relieves some of the stressed caused by rapid cooling in the hardening process.
( )6.The addendum circle of the external gear is smaller than its dedendum circle.
Ⅲ.Answer the following questions briefly according to the text.
1.Which two kinds are typical drawings in machine manufacturing divided into?
2.What is the application of malleable cast iron?
3.What is the carbon content of medium carbon steel?
4.What’s definition of the strength?
5.What is the function of the normalizing?
Part B
Reading Material Annealing Types
Annealing consists of heating steel slightly above its critical range and cooling very slowly.Annealing relieves internal stresses and strain caused by previous heat treatment,machining,or other cold working processes.The type of steel governs the temperature to which the steel is heated for the annealing process.The purpose for which annealing is being done also governs the annealing temperature.
There three types of annealing processes used in industry are full annealing,process annealing,and spheroidizing.
Full annealing is used to produce maximum softness in steel.Machinability is improved.Internal stresses are relieved.Process annealing is also called stress relieving.It is used for relieving internal stresses that have occurred during cold-working or machining processes.Spheroidizing is used to produce a special kind of grain structure that is relatively soft and machine-able.This processes generally used to improve the machine-ability.