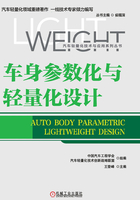
1.1 车身的分类与组成
1.1.1 车身的分类
车身是汽车重要的组成部分,是汽车四大总成之一。其基本功能是将汽车各组成部件集成连接在一起形成一个整体,并为乘员或物品提供容纳空间,如图1-1所示。车身对整车的动力性、燃油经济性、行驶平顺性、操纵稳定性以及空气动力学等性能起着至关重要的作用。车身结构开发涉及材料、制造工艺、结构设计等诸多领域,其开发水平是汽车企业的核心竞争力之一,也体现一个国家的工业水平和完备程度。

图1-1 典型白车身结构
汽车车身有多种结构形式,按照承载方式的不同,可将汽车车身分为非承载式车身与承载式车身,如图1-2所示,以及介于两者之间的半承载式车身。

图1-2 车身结构形式
1. 非承载式车身
具有非承载式车身(图1-2a)的汽车一般含有刚性车架,车身、动力总成与油箱(燃油车)/动力电池(电动车)、车桥与悬架等总成安装在车架上。其中,车身一般通过柔性衬垫与车架连接。此时,由于车身对整车承载贡献率较小,可以认为车身仅仅起到安装与容纳功能,不参与整车承载。这里的刚性车架并非是完全刚性的,车身还是要受到通过车架的安装结构传递的载荷。由于车架刚度较大且远远大于车身刚度,使得相对于车架,车身承受的整车载荷较小。
图1-3是具有车架的非承载式车身主体与车架。发动机、传动系、行驶系、转向系和其他底盘附件等牢固地安装在车架上,车身通过悬置与车架连接。作用在汽车上的载荷主要由车架来承担,车身承载的载荷较小。BJ80越野车就是采用非承载式车身。
(1)非承载式车身结构的优点
1)非承载式车身结构由于具有刚强度较大的车架结构,能承受更大的负载,同时也可承受更大的来自路面的载荷,因此具有非承载式车身结构的汽车一般承载能力和通过性更好。
2)动力总成、悬架等总成安装在刚度较大的车架上,车架则一般通过柔性橡胶衬套与各总成连接。这样,车架起到了隔离来自发动机与路面激励的作用,此两者均是汽车的主要激振源。车架在一定程度上提高了乘坐舒适性。另外,车架的存在减小了车身所承载的力,也起到延长车身使用寿命的作用。

图1-3 非承载式车身结构示意图
3)车架是汽车承载能力的基础,车身相对独立地安装在车架上,便于生产过程中的装配工序和使用过程中的维修处理。车身的这种独立性,使得车型的衍生变得更加容易,根据需要对车身进行适当变形,即可得到不同车型,丰富了产品系列,满足了市场的不同需求。
(2)非承载式车身的缺点
1)由于车身不参与整车承载,仅车架承受整车载荷,无法形成空间框架的承载结构,如需保证车架强度、刚度和整车承载能力,车架的质量往往会非常大,不利于整车轻量化。
2)车身下方安装有刚性车架,不利于整车布置与空间的有效利用。
小结 大中型商用车由于承载性能需求较大,或者由于功能需求使得车身无法形成封闭腔体,往往采用非承载式车身;对于中高级乘用车,其发动机重量大、轴距较长、附加设备多,整车整备质量相应增大,此时也常采用非承载式的车身形式。总的来讲,鉴于非承载式车身的车辆具有上述利弊,此类车身常见于中大型车辆。
2 . 承载式车身
承载式车身(图1-2b)则无刚性车架,车身是由下车体的前后纵梁、门槛梁、若干横梁,以及从上车体的A柱到D柱、上边梁和顶盖横梁等腔体结构梁组成的框架式结构,并与钣金覆盖件焊接组成有机整体。发动机与底盘零件、备胎以及其他相关附件直接安装在车身上,此时,车身除了具有安装和容纳功能外,还是整车的主要承载结构。
承载式车身没有刚度和强度较高的车架,是由车身结构承受所有的整车载荷。为了满足整车操纵稳定性、基本NVH[1]性能与行驶平顺性的要求,车身结构必须达到更高的刚度与强度性能指标。并且在发动机、底盘零件的安装位置还应做相应的加强结构以提高这些位置的耐久性。因此,在车身结构设计上承载式车身应比非承载式车身更强,承载式车身可以看成车架与非承载式车身稳固焊接在一起的整体。
(1)承载式车身结构的优点
1)车身本身形成完整的框架式承载结构,可充分利用三维承载空间,提高承载效率。从结构设计上来看,有利于集成式结构设计开发,将车身框架结构设计成多环状的封闭空间布置形式,可进一步提高承载效率,图1-4所示为某轿车的笼式车身结构设计,能最大限度地利用材料使之充分承受来自外部扭转、弯曲及其组合载荷,达到轻量化的目的。由于省去了重量较大的车架,汽车轻量化程度大大提高,相应总体成本更低。

图1-4 某轿车笼式车身结构设计
2)由于没有车架占用底盘空间,整车空间利用率相应提升,因此在相同整车尺寸条件下,承载式车身室内空间可以设计得更大,地板高度可以更低,同尺寸条件下进出性更好。
(2)承载式车身的缺点
承载式车身结构主要采用冲压件点焊拼接而成,零件较多,不适合用于长轴距重载的车型。车身与发动机和悬架直接相连,路面和发动机激励更容易传递到车身上产生影响乘坐舒适性的噪声与振动。为降低这种影响,车身需进行更合理的结构设计,并增加隔振、减振材料,这在一定程度上增加了开发成本。
基于轻量化与空间利用率的考虑,此类车身常见于中小型乘用车。
3. 半承载式车身结构
半承载式车身结构是一种过渡性的车身结构形式,这种车身还是安装在车架上,但是车架刚度较非承载式车身的车架刚度小,车身参与承载的程度较非承载式车身高。这类车身可见于部分大客车结构中。
1.1.2 车身的组成
广义上的汽车车身,包含金属白车身(Body in White, BIW)、开闭件以及相关附件,本书研究的车身参数化建模与概念设计主要针对白车身结构件,因此本书在介绍车身组成时,仅指白车身结构件。
以乘用车为例对车身结构组成进行说明,根据车身用途、造型风格与厢体数量的不同,车身结构与组成差异较大,相应的命名也有所不同。本书采用行业较为通用的词汇对主流汽车结构进行拆分以便阅读。
无论承载式还是非承载式车身,目前主流的白车身主要由金属板状结构连接而成;钣金件与钣金件之间形成带腔体的梁状结构,梁与平板结合组成整个车身。在梁与梁相交的位置形成复杂的接头结构,如A柱接头、B柱接头等。这些梁与接头的结构设计与布置位置对于白车身结构性能往往起着至关重要的作用。
如前所述,车身是由众多钣金件连接(焊接或铆接等)而成,根据连接关系可以进行结构拆分。合理的结构拆分有利于优化车身连接生产工艺,有利于提高模块化设计与制造水平。图1-5为某合资车型的车身结构拼接顺序,可以看出整个白车身结构由下车体总成与上车体总成焊接而成。下车体焊接顺序是先将前舱、前地板与后地板分别焊接成整体,然后拼接成下车体总成。上车体则是由前侧围内板、后侧围内板与外板总成(含加强板)拼接成侧围总成,加上顶盖总成制成上车体总成。上、下车体总成最后拼接成完整的白车身总成。

图1-5 车身结构拼接顺序
从结构设计来看,上车体与造型风格、厢体形式的关联度更紧密。通过更改上车体结构形式与零件位置可以进行造型变化,形成不同数量的厢体。上车体与下车体围合形成乘员舱和行李舱,其尺寸与结构对乘坐空间与行李舱容积、乘员进出性和驾驶员视野等性能影响较大。同时,作为白车身的重要组成部分,上车体结构对车身刚度和模态等性能也有较大影响。因此,进行上车体结构开发时,要在外造型的约束下,尽可能地增大上述的厢体空间,符合布置与安装功能要求,满足结构刚度、强度的要求。
而下车体或车架则主要用于安装动力总成及冷却模块,悬架、转向机构、油箱、备胎等底盘结构和附件总成,以及座椅与仪表板等内外饰总成,并承受这些总成所传递的载荷。因此,下车体应该有足够的刚度与强度,在安装位置附近,还要设计加强结构来保证足够的安装刚度与强度。下车体也是碰撞过程中主要的吸能结构,对整车安全性能影响巨大。下车体与动力总成、底盘等安装总成的组合是汽车基本功能件,对整车使用性能影响也是巨大的,这些总成通过组合形成的整体可称为汽车平台。在汽车平台化开发过程中,平台往往可以为不同车型所共用,或者仅需做少量更改便可达到共用的目的,通过平台化开发可减少开发周期与成本。
图1-6为某白车身与其上、下车体结构组成示意图。上车体总成包含侧围总成、顶盖外板、顶盖横梁、衣帽架总成和后围总成。

图1-6 白车身与其上、下车体结构组成
1. 车身侧围结构
车身侧围结构主要由侧围框架、后轮罩以及相关加强结构刚性连接而成。侧围框架则主要由A柱、B柱、C柱、D柱、门槛梁和顶盖边梁等组成,如图1-7所示。

图1-7 典型的车身侧围框架结构
(1)A柱 侧围各位置的结构有不同的功能与性能要求。A柱上部需要安装前风窗玻璃,其截面大小对驾驶员视野盲区有重要影响。为减少由A柱产生的视野盲区,其梁截面应尽可能地做窄。然而,在正面碰撞过程中,A柱上边梁是一条重要能量传递路径。过窄的A柱在碰撞过程中容易发生屈曲,影响安全性能。A柱下部分需安装侧前门和仪表板横梁,在正面碰撞过程中,需承受通过前围横梁传递的碰撞能量。并且A柱对车身整体的结构刚度也有一定影响,需要综合考虑进行设计。
(2)B柱 B柱由B柱内板、外板与加强板连接而成。B柱上安装有侧前门锁扣与侧后门铰链,并起着支撑前、后侧门的作用。由于车身整体造型的需要,B柱上、下截面变化较大,一般呈现上小下大的结构形状。在性能上,B柱对整车侧面碰撞性能影响较大。侧面碰撞时,由于吸能空间较小,因此要求吸能结构的强度要大;且由于空间受限,B柱常采用高强度级别的材料(如高强度钢和热成形钢等)以提高其结构强度、刚度与碰撞性能。
(3)C柱 C柱上部分隔离后侧窗与后门洞形成立柱,下部分由后轮罩与侧围外板形成腔体。在功能上,C柱上需安装后门锁扣。通常,C柱通过轮罩和侧围外板与下车体和后侧围连接,相对增加了结构连接的强度和刚度。
(4)顶盖边梁 顶盖边梁连接着上述各立柱,与立柱交叉形成相应的接头结构。顶盖边梁上需要安装顶盖总成,对顶盖起重要的支撑作用。在性能上,顶盖边梁对车身结构刚度和抗顶压性能影响较大,在正面和侧面碰撞中能分散碰撞能量,因此截面设计不宜过小。
(5)门槛梁 门槛梁是上、下车体之间连接的重要组成部分,与各立柱组成侧围完整的框架结构。门槛梁结构强弱对车身刚度影响很大,尤其是弯曲刚度。在侧面碰撞过程中,门槛梁也起到关键的吸能和抗冲击作用,应具有足够的强度来抵抗撞击产生的变形。在正面碰撞中,门槛梁也起到重要的冲击载荷传递作用,因此在结构设计中应适当增加门槛梁内部加强结构,以满足各项相关性能的要求。
2. 车身顶盖结构
顶盖是车身重要的覆盖件结构,受车身尺寸、造型和乘员舱空间的限制,车身顶盖结构往往设计得比较薄,其上的加强结构占用空间也非常有限。在顶盖设计中,可以形成较大腔体结构的零件主要有顶盖前横梁和顶盖后横梁。顶盖前横梁一般会安装前风窗,对风窗局部模态性能有直接影响;三厢车后横梁一般安装后风窗,其重要性与前横梁类似;两厢车后横梁会安装尾门铰链,并形成尾门洞结构,对车身扭转刚度与模态都有非常重要的影响。
根据配置的需要,顶盖上可能安装有不同尺寸的天窗,如图1-8所示,此时需设计对应的加强安装结构。由顶盖横梁、前后横梁、顶盖外板组成的总成,若与侧围框架形成对应的环状结构,则有利于提高车身的结构刚度、模态频率和碰撞等各项性能。在白车身设计和优化时,应尽可能地保持环状结构的完整性,提高材料利用率。

图1-8 无天窗顶盖与全景天窗顶盖
由于造型、空间和驾驶员视野,以及乘员进出性等美观与人机工程性能需求,上车体各结构的尺寸受限,这种趋势越来越明显。由于空间上对上车体的限制,在进行结构设计时,应更加注重下车体结构的加强设计。一般来讲,承载式车身的下车体结构是其主要的承载结构,同时也属于平台总成,当进行平台开发时,需同时满足不同车型对各项性能的要求,因此经常采用纵横梁交错结构,保证既满足功能需求,又能达到规定的性能要求。下车体一般可分为前舱总成、前地板总成和后地板总成,如图1-9所示。
3. 前舱总成结构
前舱即发动机舱,对于具有承载式车身的汽车而言,前舱总成结构需要安装动力总成、冷却水箱和风扇等舱内零件,也需安装前副车架与前悬架等底盘结构。结构上,从前到后一般可分为水箱框架(上、下支架)、前纵梁及其延伸梁、减振塔支座、前围横梁与前围板等子总成,如图1-10所示。

图1-9 下车体总成的结构组成

图1-10 前舱总成结构分解
分析和测量白车身弯扭刚度时的加载或约束位置一般设在前舱,因此前舱结构对白车身刚度的影响是巨大的。前舱是整车正面碰撞过程中重要的吸能结构,在100%正碰中约占到总吸收能量的70%,结构设计上应与整车碰撞总能量进行相应匹配,并设计相关压溃与吸能环节,实现合理的变形属性、吸收碰撞冲击产生的动能。前舱也是发动机和底盘的安装位置,需传递发动机和底盘传递过来的激励与载荷,因此其局部安装刚度和耐久性能也是需要重点考虑的问题,以降低结构疲劳破坏风险。
4 . 前地板总成结构
前地板总成在下车体的中间位置,与上车体前围等总成围合成完整的乘员舱,其上一般需要安装前排座椅与前后连通的管路线束等零件。前地板总成如图1-11所示,主要分为地板平板、座椅安装横梁(前、后横梁)和可能有的中央通道及其加强结构。
前地板是乘员舱的主要组成部分,也是乘员直接接触到的主要部位,前排座椅安装在座椅横梁上,乘员从此处感受地板垂向变形和外部传递来的振动,因此地板局部刚度和座椅安装刚度是非常重要的。较好的局部结构有利于降低汽车行驶过程中乘员的垂向位移和接触位置的振动感受,提高乘坐舒适性。座椅横梁也是侧面碰撞过程中重要的承载结构,提高其侧向压溃性能有利于在侧面碰撞过程中保持乘员舱完整,保护乘员安全。
5 . 后地板总成结构
后地板总成处于下车体后端,是行李舱或备胎舱的主要组成部分,对于承载式车身结构,其上需要安装后副车架与悬架、油箱、备胎以及后座椅等总成结构。后地板总成一般包含后地板与备胎舱大板、后轮罩总成、后横梁总成与后纵梁总成等,如图1-12所示。

图1-11 前地板总成结构分解

图1-12 后地板总成结构分解
后地板总成上安装有后副车架和后悬架等底盘结构,将后轮载荷传递到车身上,在分析和测量车身刚度时一般在此总成上设置约束位置,因此其结构对车身整体刚度影响较大。后地板也是行李与备胎的承载结构,因此结构上也应满足相应的要求。在追尾碰撞过程中,后地板结构尤其是后纵梁结构,应设计达到一定强度和刚度,以保护后排乘客乘坐的舒适性和油箱结构的安全性。