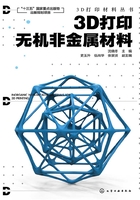
2.2.3 激光选区烧结成形坯体特点与热处理
激光选区烧结(SLS)成形后得到的是由黏结剂黏结陶瓷粉体形成的坯体,由于在成形阶段粉体仅靠少量的黏结剂黏结且粉体堆积密度较低,得到坯体相对密度仅有30%左右,具有多孔疏松的特征。若要获得高致密度的陶瓷零件,需要对SLS坯体进行后处理,常用的后处理方法包括浸渗、冷等静压(CIP)、热等静压(HIP)等[24,25]。Lee[26~29]采用硅溶胶等对Al2O3素坯进行浸渗,最终获得了相对密度80%的Al2O3陶瓷。Liu等[30]将SLS技术和冷等静压技术(CIP)结合来制造致密陶瓷。首先,采用SLS技术制造出Al2O3素坯,随后对其进行冷等静压处理,经排胶和高温烧结后,成功制造出Al2O3齿轮等复杂陶瓷零件,其相对密度大于92%、抗弯强度大于100MPa。Chen等[31]通过SLS/CIP制备出复杂形状的生物ZrO2全瓷修复体,SLS/CIP复合成形得到的ZrO2陶瓷素坯形状完整,无破裂、弯曲等缺陷。在烧结温度为1500℃时,相对密度达到86.65%,抗弯强度为279.50MPa。图2-15为牙齿模型和SLS/CIP复合工艺制作的全瓷修复体。Shahzad等[32]采用SLS技术制造出Al2O3素坯,发现经高温烧结后,样品相对密度很低。为了提高其相对密度,对SLS制造Al2O3素坯进行热等静压处理,大幅提高了Al2O3陶瓷的致密度(达到88%)。

图2-15 采用SLS/CIP复合技术制备ZrO2全瓷修复体[31]
(a)牙齿模型;(b)陶瓷牙
SLS制造陶瓷的原理决定了采用该方法只能制造出多孔陶瓷,如需制造致密陶瓷则需要经过冷等静压等后处理工艺来实现。若采用SLS技术直接制造多孔陶瓷则会更有优势。魏青松等[33]直接采用SLS技术制造出复杂结构多孔堇青石陶瓷。陈敬炎等[34]采用机械混合法制备适于SLS成形的煤系高岭土/黏结剂复合陶瓷粉体,然后利用SLS技术制造煤系高岭土多孔陶瓷。通过优化SLS工艺参数和高温烧结工艺参数,制备出性能较为优良的煤系高岭土多孔陶瓷。然而,由于陶瓷粉体与黏结剂的密度、粒径大小等差别较大,采用机械混合法制备的复合陶瓷粉体中黏结剂很难均匀分布于陶瓷粉体中,从而影响SLS成形效果和最终制造多孔陶瓷的性能。
为了改善采用SLS技术制备多孔陶瓷的力学性能,Chen等[35]提出一种新型的双层包覆法。他们首先采用化学共沉淀法,在煤系高岭土粉体表面包覆MnO2烧结助剂。通过KMnO4溶液和MnC4H6O4·4H2O[Mn(Ac)2·4H2O]溶液发生化学反应得到MnO2烧结助剂,经过抽滤、烘干、碾磨过筛等即可得到MnO2包覆高岭土的复合陶瓷粉体。然后,再采用溶剂蒸发法在制得粉体表面包覆酚醛树脂黏结剂。将上述MnO2包覆的煤系高岭土粉体与酚醛树脂放入烧杯中,加入足量的无水乙醇溶液,在加热的条件下搅拌至少量无水乙醇,然后经烘干、碾磨过筛,即可得到助烧剂和高分子黏结剂均匀包覆的复合陶瓷粉体(见图2-16)。当没有MnO2烧结助剂时,煤系高岭土多孔陶瓷中可见大量的孔隙和细小颗粒,陶瓷颗粒之间的烧结颈面积很小,结合强度较差。当Mn(Ac)2·4H2O溶液量上升到18mL时,煤系高岭土多孔陶瓷微观结构变化显著,微观孔隙和细小颗粒大量减少,陶瓷颗粒之间的烧结颈面积增大,结合强度增大。这是由于在高温烧结时,MnO2烧结助剂可以形成合适的液相从而促进颗粒的重排和传质过程。当Mn(Ac)2·4H2O溶液量从0增加到18mL时,煤系高岭土多孔陶瓷的抗压强度从0.82MPa增加到17.38MPa,而显气孔率从64.10%下降到48.74%。Chen等最后成功采用SLS技术制备出具有纵向贯通孔和横向交叉孔的煤系高岭土多孔陶瓷(见图2-17)。

图2-16 采用SLS技术制备煤系高岭土多孔陶瓷流程示意图[35]

图2-17 SLS技术制备的煤系高岭土多孔陶瓷[35]
(a)多孔陶瓷模型;(b)多孔陶瓷
基于SLS技术的成形原理可知,采用SLS技术制备具有复杂孔道的多孔陶瓷具有明显优势。在SLS成形过程中,复合陶瓷粉体性能对SLS成形陶瓷零件性能有较大影响。为了实现SLS成形过程中良好的铺粉效果,一般要求用于SLS成形的陶瓷粉体具有良好的流动性和合适的粒径分布。传统SLS成形技术中采用的Al2O3、ZrO2等陶瓷粉体,都需要首先通过造粒等方法使其具有良好的流动性和合适的粒径,工艺过程相对复杂。近年来,一种新型的多孔陶瓷材料——陶瓷空心球逐渐被用来制备新型的多孔陶瓷。陶瓷空心球尺寸可控、成分可调、球形度高,满足SLS成形的要求,是一种可以用于SLS成形的理想原材料。目前人们已经提出采用SLS技术制备陶瓷空心球的方法,并且引入烧结助剂来进一步提高多孔陶瓷的力学性能。该方法将SLS技术和陶瓷空心球结合起来,利用陶瓷空心球本身的气孔和SLS成形过程中形成的孔隙,可以制备出高孔隙率的复杂结构多孔陶瓷。陶瓷空心球满足SLS成形的要求,其成分和孔隙率可控,从而使最终成形的多孔陶瓷性能可控。同时,引入烧结助剂将会进一步提高多孔陶瓷的力学性能。
Chen等[36]采用机械混合法制备出粉煤灰空心球-PA12复合陶瓷粉体,通过SLS技术制备出高孔隙率多孔莫来石陶瓷。随着烧结温度从1250℃上升到1400℃,多孔莫来石陶瓷的抗压强度从0.2MPa增加到6.7MPa,而孔隙率由88.7%降低到79.9%。多孔莫来石陶瓷抗压强度的增加与烧结颈强度的增加有密切的关系,随着烧结温度的增加,多孔莫来石陶瓷的断裂机制由沿空心球断裂变为穿过空心球断裂(见图2-18)。当然烧结颈强度越高,空心球聚集得也就越密,空心球间的空隙减小,且烧结温度越高,空心球内部空隙也收缩得更小,导致孔隙率降低。

图2-18 多孔莫来石陶瓷在不同烧结温度下的断裂方式示意图[36]
(a)烧结温度低于1350℃;(b)烧结温度高于1350℃
为了进一步改善基于粉煤灰空心球的多孔莫来石陶瓷的SLS成形效果,Chen等[18]采用溶解沉淀法制备出PA12覆膜的粉煤灰空心球粉体,并在不同温度烧结得到多孔莫来石陶瓷。由图2-19可知,多孔莫来石陶瓷的孔主要有两类:空心球内部的孔和空心球之间的孔。随着烧结温度从1250℃上升到1400℃,空心球之间的结合强度不断增加,其断裂形式由沿球断裂逐渐转变为穿球断裂。另外,Chen等[37]还研究了采用SLS制备基于粉煤灰空心球的多孔莫来石陶瓷力学性能的增强机制,认为空心球壁结构致密增厚和空心球之间增强的烧结颈是制备多孔莫来石陶瓷性能增强的主要原因。

图2-19 不同温度烧结的多孔莫来石陶瓷SEM图[18]
(a)1250℃;(b)1300℃;(c)1350℃;(d)1400℃
粉煤灰空心球成本低,但由于其成分较为单一,不能用于制备其他成分的陶瓷。另一类人造的陶瓷聚空心球逐渐引起了人们的重视。陶瓷聚空心球的大小、成分等可以通过调整制备工艺来进行设计,从而可以有效控制多孔陶瓷的孔径大小、气孔率等性能,且可以用来制备多种多孔陶瓷。Liu等[38]采用机械法制备Al2O3聚空心球/环氧树脂E12复合陶瓷粉体,利用SLS制备出Al2O3聚空心球陶瓷。图2-20为不同温度烧结的Al2O3聚空心球陶瓷的SEM图。可以看出Al2O3聚空心球仍然保持良好的球状,不同Al2O3聚空心球之间存在较多孔隙。随着烧结温度的升高,Al2O3聚空心球陶瓷中的Al2O3晶粒逐渐长大。随着烧结温度从1500℃升高到1650℃,Al2O3聚空心球陶瓷的孔隙率由77.09%减小到72.41%,抗压强度由0.18MPa升高到0.72MPa。

图2-20 不同温度烧结的Al2O3聚空心球陶瓷的SEM图[38]
(a)、(b)1500℃;(c)、(d)1550℃;(e)、(f)1650℃
研究表明,SLS制备出Al2O3聚空心球陶瓷的力学性能较低。为了提高Al2O3聚空心球陶瓷的力学性能,刘珊珊[16]采用化学共沉淀法在Al2O3聚空心球粉体表面包覆CaSiO3助烧剂,促进烧结致密化过程。首先将1200℃预煅烧后的Al2O3聚空心球加入到1.5mol/L Na2SiO3溶液中充分混合,随后将配制好的1.5mol/L的CaCl2溶液逐滴加入混合液中继续充分混合,最后将混合溶液进行抽滤、干燥、过筛后获得包覆CaSiO3的Al2O3聚空心球粉体。在此基础上,采用机械混合法制备出适用于SLS成形的Al2O3聚空心球-E12复合陶瓷粉体(加入12%的黏结剂E12),在最优的工艺参数下,采用SLS技术制备出Al2O3聚空心球陶瓷。图2-21为Al2O3聚空心球陶瓷的孔隙率和抗压强度与CaCl2溶液加入量的关系曲线图。随着助烧剂包覆含量的增加,Al2O3聚空心球陶瓷的孔隙率逐渐降低而抗压强度大幅增大,其孔隙率由77.03%减小到68.16%,而抗压强度由未包覆CaSiO3助烧剂时的0.29MPa增加到8.39MPa。Al2O3聚空心球陶瓷的孔隙由Al2O3聚空心球内部自身的孔洞和Al2O3聚空心球之间的间隙组成。随着助烧剂含量的增加,Al2O3聚空心球陶瓷烧结致密化,Al2O3聚空心球之间的间隙逐渐减少,Al2O3聚空心球自身也更加致密,不同Al2O3聚空心球之间的界面结合明显增强,最终使Al2O3聚空心球陶瓷的孔隙率降低,抗压强度得到大幅提高。因此,采用化学共沉淀法在Al2O3聚空心球表面包覆CaSiO3助烧剂可以有效改善Al2O3聚空心球陶瓷的性能。

图2-21 Al2O3聚空心球陶瓷的孔隙率和抗压强度与CaCl2溶液加入量的关系曲线图[16]