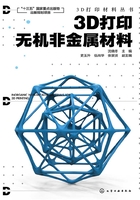
2.3.2 光固化成形过程
2.3.2.1 光固化成形技术的发展与原理
1981年,日本名古屋市工业研究所的小玉秀男发明了利用紫外光硬化聚合物的方法制备三维塑料模型,其紫外线照射面积由掩模图形或光线发射机控制。1984年,美国UVP公司Hull开发利用紫外激光固化高分子光聚合物树脂的光固化技术,1986年获得专利。Hull基于该技术创立世界第一家3D打印公司(3D Systems),并于1988年推出第一台商品化3D打印设备(SLA250)。同期,日本的CMET和SONY/D-MEC公司也分别在1988年和1989年推出了各自的商品化光固化(SL)设备。1990年,德国光电公司(EOS公司)出售了他们的第一套SL设备,1997年将该SL业务售给3D Systems公司,但EOS仍然是欧洲最大的SL设备生产商。2001年,日本德岛大学研发出了基于飞秒激光的SL技术,实现了微米级复杂三维结构的3D打印[56]。
进入21世纪后,SL技术发展速度趋缓。此时SL在应用领域中主要分两类:一类是针对短周期、低成本产品验证,如消费电子、计算机相关产品、玩具手板等;另一类是制造复杂树脂构件,如航空航天、汽车复杂零部件、珠宝、医学零件等。但是,高昂的设备价格一直制约着SL技术的发展。2011年6月,奥地利维也纳技术大学Markus Hatzenbichler和Klaus Stadlmann研制了世界上最小的SL打印机,仅有牛奶盒大小,重约3.3lb(1lb=0.4536kg)。2012年9月,美国麻省理工学院研究出一款新型SL打印机——FORM1,可制作层厚仅为25μm的物体,这是当时精度最高的3D打印方法之一。2016年4月意大利Solido 3D公司开发了基于手机LED屏幕的DLP光固化打印机,成形尺寸为7.6cm×12.7cm×5cm,成形精度可达0.042mm。该产品使用手机LED屏幕取代传统DLP打印机需要的投影仪,将设备成本大幅降低。国内西安交通大学从20世纪90年代初开始研发SL技术,开展产业化生产和销售工作。上海联泰科技有限公司则专门从事生产和销售SL设备。近期则出现了一大批研发桌面级SL设备的企业,如浙江讯实科技有限公司。
光固化成形是3D打印技术中被广泛应用的一种方式,根据单层固化方式不同,光固化成形技术可以分为立体光固化(SL)技术和数字光处理(DLP)技术两种。SL和DLP 3D打印基本技术流程如图2-25所示:相对于其他3D打印技术,光固化成形技术采用激光束或者数字微镜控制打印区域,在制备复杂形状、高精度零部件方面有较大优势。目前,光固化成形技术在陶瓷精密制造领域已取得比较好的研究成果,并且探索其在航天、汽车、生物医疗等领域的应用。

图2-25 SL和DLP 3D打印基本技术流程[56]
(1)立体光固化成形技术
立体光固化成形技术是主流3D打印方法之一,其基本原理如图2-26(a)所示。首先,通过控制激光器向下发出激光束,选择性照射材料槽中最上层的光敏树脂,由点到线再到面,完成树脂单层固化;然后,控制工作台下降,将光敏树脂涂覆于零件上表面,继续进行下一次固化;重复上述的固化过程,直到获得最终的实体模型。该技术早期主要是针对光敏树脂材料的快速成形,直到20世纪90年代Griffith首先提出将光固化成形技术与陶瓷材料制备技术相结合,并提出了基于SL技术的陶瓷浆料要求。与其他3D打印技术相比,SL技术具有巨大的优势。第一,SL技术使用直径小的激光束(通常在几十微米左右),制备的陶瓷坯体精度非常高,一般能够实现高达10~50μm的成形精度;第二,SL技术的适应性强,几乎适用于任何陶瓷粉体,在采用紫外光实现光固化之前,本质上陶瓷-光敏树脂浆料与传统陶瓷胶态成形思路完全一致,原则上只需要能够制备出陶瓷-光敏树脂浆料,就能够进行下一步的光固化成形;第三,成形坯体内应力小、均匀度高,通过后处理可获得高性能陶瓷零件。

图2-26 光固化成形技术示意图
(a)SL技术[48];(b)DLP技术[57]
此外,由于SL技术直接光固化成形浆料、再经高温热处理得到陶瓷材料与构件,这为先驱体转化陶瓷提供了崭新的思路:采用陶瓷先驱体使用SL技术直接成形出相应的陶瓷先驱体预制体坯体,经过高温裂解后得到先驱体转化陶瓷及构件。由于具有如此明显的技术优势,SL在陶瓷材料3D打印领域得到了越来越多的关注,包括奥地利、法国、美国以及国内众多科研院所、企业都开始探索陶瓷材料的SL 3D打印技术与设备的开发,纷纷采用该方式成形制备了不同种类、不同结构形式的陶瓷材料与构件(见图2-27)。

图2-27 立体光固化成形技术打印的各种陶瓷器件[58]
然而,SL技术也存在一些不足。由于大多数SL模式采用上方光源、成形台下降的打印模式,这就意味着料槽里需要大量的浆料才能够使得打印进行下去,造成了一定的浆料浪费与成本提升。因此,如果能实现下方光源、成形台上提的光固化方式,将会使得陶瓷材料基于光固化原理的3D打印技术得到更广阔的应用与推广。在此需求的驱动下,基于光固化原理的数字光处理技术得到越来越多的科研工作者与设备供应商的关注。
(2)数字光处理技术
数字光处理(DLP)技术是以美国得州仪器公司的数字微镜片(digital micromirror device,DMD)为主要关键处理元件而开发的光固化成形技术。DLP技术的工作原理与SL技术的类似[如图2-26(b)所示],但是采用了DMD装置,可使该层图像直接投影到整个区域中,实现面固化成形。SL成形方法是紫外光束由点到线再到面的成形方式,因此成形速度较慢。DLP成形则是利用紫外光将每个成形截面的形状精确投影到打印面上,成形速度更快。除此以外,DLP技术是向上提拉打印坯体,节省打印原料,且对陶瓷浆料的黏度要求不高。DLP技术的成形精度优于SL技术,其精度主要取决于DMD装置的分辨率。
2.3.2.2 光固化成形技术成形过程
陶瓷光固化成形过程是陶瓷3D打印的重要环节,其决定着陶瓷零件结构功能的实现。成形过程由三个步骤组成,分别是预处理、成形过程和后处理。
(1)预处理
所谓的预处理与光敏树脂SL/DLP成形技术的前处理相同,包括建立成形件三维模型、近似处理三维模型、选择模型成形方向、三维模型的切片处理和生成支撑结构。其流程如图2-28所示。

图2-28 数据预处理流程[56]
首先必须在计算机上,利用CAD、Solidworks等三维计算机辅助设计软件,根据产品的要求设计三维模型;或者使用三维扫描系统对已有的实体进行扫描,并通过反求技术得到三维模型。
对所得到的三维模型进行必要的调整和修改。模型确定后,根据形状和成形技术的要求选定成形方向,调整模型姿态。然后使用专用软件添加模型技术支撑,模型和技术支撑构成一个整体,并转换成STL格式的文件。
对STL格式文件进行切片处理。由于3D打印是通过一层层断面形状来进行叠加成形,因此,加工前需要使用切片软件将三维模型沿高度方向进行切片处理,提取截面轮廓的数据。切片越薄,精度越高。建议的取值范围一般为25~0.3μm,随着技术的发展,取值范围可根据光固化成形机精度进行调整。
(2)成形过程
成形过程是SL成形技术的核心步骤,其过程由模型断面形状的制作和叠加合成。3D打印系统根据切片处理得到的断面形状,在计算机的控制下,通过控制激光器向下发出激光束,选择性照射材料槽中最上层的光固化陶瓷浆料,由点到线再到面,完成陶瓷浆料单层固化;然后,控制工作台下降,将光固化陶瓷浆料涂覆于零件上表面,继续进行下一次固化;重复上述的固化过程,直到获得最终的实体模型。
对于DLP成形技术,成形过程与SL技术类似,但DLP技术常采用倒置面成形方式,即激光光源经DMD形成模型的某一截面的形状,然后对该截面形状的陶瓷浆料照射固化,液槽上方的提拉机构,每次截面曝光完成后向上提拉一定高度(该高度与分层厚度一致),使得当前固化完成的固态树脂与液槽底面分离并黏结在提拉板或上一次成形的树脂层上。这样,通过逐层曝光并提升来生成三维实体。
(3)后处理
后处理包括坯体的干燥、去支撑处理。由陶瓷浆料制成的实体模型,又称为坯体。打印完成的坯体首先需要去除支撑。树脂基陶瓷坯体无需经过干燥,经过去支撑处理后,可直接进行后续热处理。若是水基陶瓷坯体,烧结前还需经过干燥过程。最终得到等待热处理的陶瓷坯体。水基陶瓷浆料制备的陶瓷坯体,在常温空气下干燥,由于收缩不均匀,坯体会开裂。广东工业大学Wu等[59]首次采用液体干燥法,即首先将打印好的陶瓷坯体置于PEG400中,去除坯体中的水,得到待烧结的坯体。该方法干燥后的坯体未出现开裂和裂纹。西安交通大学Zhou等[60]采用SL成形技术成形二氧化硅坯体,然后通过冷冻干燥法得到待烧结的二氧化硅坯体。